Performance industrielle : définition, enjeux et exemples concrets
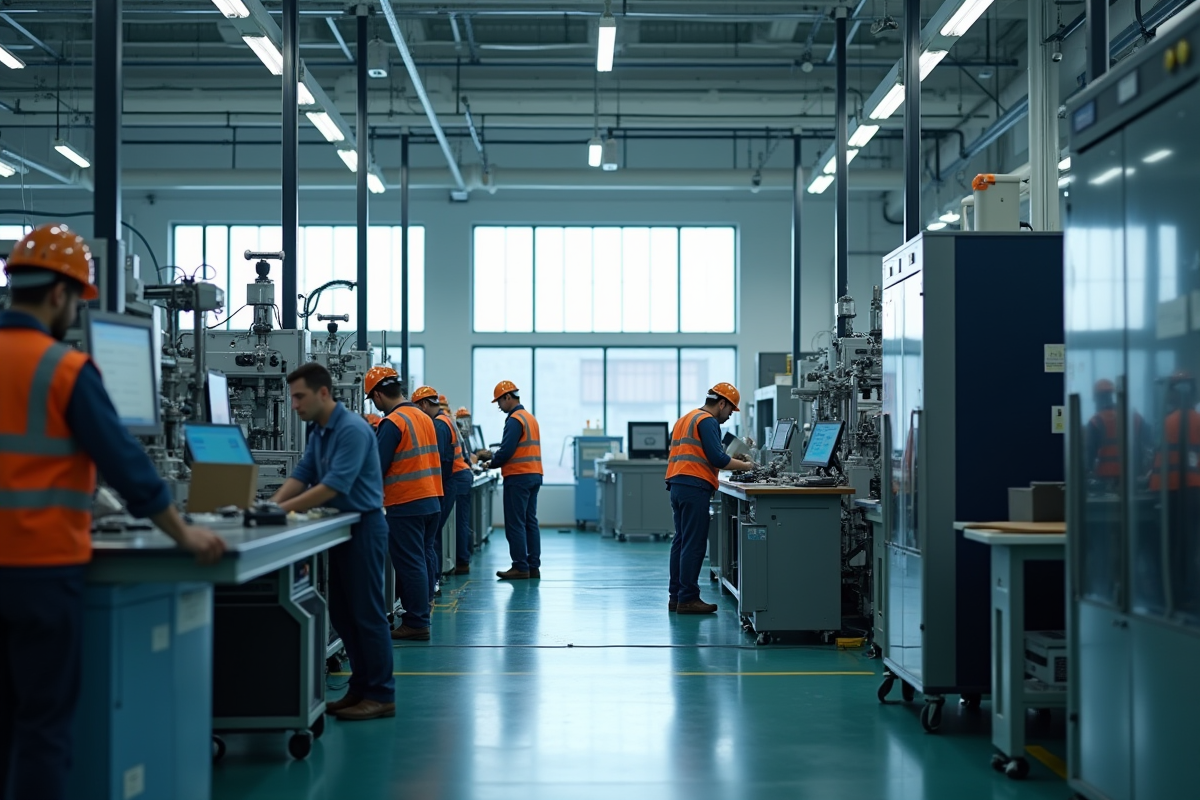
Certains sites industriels affichent des taux d’efficacité qui dépassent 90 %, alors que des entreprises comparables stagnent sous la barre des 60 %. Un même équipement peut produire deux fois plus dans une usine que dans une autre, avec des ressources identiques. L’introduction de l’IoT a permis à certains groupes de réduire de 20 % leurs arrêts non planifiés en moins de six mois.
Les écarts de résultats s’expliquent rarement par la seule technologie employée. Les méthodes d’évaluation, le suivi des indicateurs et la capacité à exploiter les données opérationnelles transforment la productivité réelle sur le terrain.
A lire également : Changement transformationnel en entreprise : définition et enjeux
Plan de l'article
- Performance industrielle : comprendre les fondamentaux et les enjeux actuels
- Quels indicateurs pour mesurer l’efficacité d’un site industriel ?
- Zoom sur l’IoT : comment les objets connectés transforment la performance industrielle
- Exemples concrets d’amélioration de la performance grâce à l’innovation technologique
Performance industrielle : comprendre les fondamentaux et les enjeux actuels
La performance industrielle ne se résume pas à une course effrénée à la production ou à la chasse aux coûts. Elle incarne la volonté d’une entreprise d’atteindre une excellence opérationnelle authentique : produire mieux, accélérer le rythme, maîtriser les coûts, sans jamais sacrifier la qualité ni la réactivité face à l’imprévu. L’objectif : transformer chaque processus de production en atout concurrentiel, tailler un avantage là où d’autres voient des contraintes.
Les directions industrielles se battent sur trois fronts : qualité, délai et coût. Pour avancer, elles s’appuient sur des méthodes d’amélioration continue telles que le Lean Manufacturing, le Six Sigma, le Kaizen ou le TPM (Total Productive Maintenance). Chacune de ces approches cible un chantier précis : éliminer les gaspillages, réduire la variabilité, gagner en fiabilité machine, ou instaurer une culture du progrès permanent.
A lire aussi : IA en 2025 : Comment les affaires seront impactées par l'intelligence artificielle ?
L’optimisation des processus guide chaque décision, mais attention à ne pas franchir la ligne rouge. Chercher la perfection à tout prix finit par figer l’organisation, brider l’agilité industrielle et parfois même détériorer la qualité. À l’opposé, négliger l’optimisation condamne l’entreprise à voir ses marges s’évaporer, alors que chaque point de productivité pèse dans la balance.
Principaux leviers de la performance industrielle
Voici les grands axes sur lesquels s’appuient les sites industriels pour booster leur performance :
- Déployer les méthodes d’amélioration continue adaptées à la réalité de l’usine
- Mobiliser tous les acteurs, du terrain jusqu’aux plus hauts niveaux
- Surveiller en permanence les risques de dérapage, entre excès de contrôle et relâchement
Cette quête de performance industrielle repose sur un subtil dosage d’optimisation, d’ajustement constant et d’alignement sur les objectifs stratégiques de l’entreprise.
Quels indicateurs pour mesurer l’efficacité d’un site industriel ?
Dans l’univers industriel, la performance s’évalue à travers des chiffres concrets, analysés à la loupe par la direction comme par les équipes terrain. Les KPI (indicateurs clés de performance) guident les décisions, orientent les efforts, et révèlent les marges d’ajustement. Au centre, le TRS (taux de rendement synthétique) fait figure de référence : il traduit le rapport entre la production conforme et le potentiel théorique des équipements, condensant en un chiffre la qualité, la disponibilité et la productivité.
Autour de ce pilier, d’autres indicateurs complètent le tableau. Le TRG (taux de rendement global) prend en compte tous les arrêts, planifiés ou non, pour donner une vision plus large de la performance globale du site. Le TPG (taux de productivité globale) compare la production obtenue aux ressources mobilisées, qu’il s’agisse de personnel ou de machines. Ces mesures ne se limitent pas à des pourcentages : elles dévoilent les potentiels inexploités, détectent les failles, et servent de base à toute démarche de progrès.
Sur le plan opérationnel, la qualité s’exprime à travers le taux de rebut, chaque pièce écartée du flux est scrutée, analysée. À l’inverse, le taux de qualité récompense les produits irréprochables. Pour compléter le diagnostic, le taux d’utilisation met en lumière l’utilisation réelle des machines par rapport à leur capacité théorique.
Les tableaux de bord centralisent l’ensemble de ces données, offrant un état des lieux immédiat. Cette visibilité alimente toute démarche d’amélioration continue, de la gestion des flux à la maîtrise des coûts, sans oublier la satisfaction du client final.
Zoom sur l’IoT : comment les objets connectés transforment la performance industrielle
Dans les ateliers d’aujourd’hui, l’internet des objets (IoT) redéfinit les standards de performance industrielle. Grâce aux capteurs, aux automates et aux machines-outils connectés, la circulation de l’information devient instantanée, précise, ininterrompue. La digitalisation ne se limite plus à quelques logiciels : elle irrigue chaque étape, chaque poste, chaque minute du processus de production.
Avec l’IoT, la collecte de données s’amplifie, offrant de nouveaux leviers pour piloter et optimiser l’activité. Les équipes tirent parti d’outils de management visuel et de la remontée automatisée des KPIs. Une défaillance n’attend plus la réunion du lundi matin : elle déclenche une alerte immédiate, directement issue d’un capteur. La maintenance prédictive s’impose comme une évidence, permettant d’anticiper les pannes, de réduire les temps d’arrêt, et de préserver la production.
L’industrie 4.0 va plus loin encore, en introduisant les jumeaux numériques et la réalité augmentée. Les opérateurs disposent d’instructions digitales contextualisées et de supports interactifs, facilitant la formation et le transfert de savoir-faire sur le poste. Des solutions telles que celles de Picomto digitalisent les modes opératoires, suivent les indicateurs, et accompagnent la montée en compétences.
Voici comment l’IoT révolutionne l’atelier moderne :
- Collecte et analyse de données en temps réel
- Maintenance prédictive
- Instructions digitales et formation interactive
- Optimisation continue du processus de production
La réactivité et l’agilité industrielle atteignent alors un nouveau palier, portées par la puissance de l’analyse instantanée et la fluidité de l’information partagée à tous les niveaux.
Exemples concrets d’amélioration de la performance grâce à l’innovation technologique
Dans les usines où la performance industrielle se vit au quotidien, l’innovation se matérialise dans les pratiques concrètes. L’adoption d’un management participatif bouleverse les routines : chaque suggestion venue du terrain, chaque expérience partagée, vient nourrir l’amélioration continue. Les opérateurs ne subissent plus le changement, ils en deviennent les architectes. Les anomalies ne s’accumulent plus dans les carnets de bord, elles sont signalées et analysées en temps réel. Les données collectées orientent les choix de maintenance et pilotent la production, sans délai.
La formation ne s’arrête plus à l’embauche. Elle irrigue toute la chaîne, portée par des supports numériques interactifs, ajustés à chaque poste. Cette dynamique d’apprentissage permanent renforce l’implication des collaborateurs et sécurise la qualité des gestes techniques. Conséquence directe : moins de rebuts, une amélioration du rendement premier passage, et des clients plus satisfaits.
La digitalisation s’invite également dans la gestion des flux, des stocks, des ordres de fabrication. Les logiciels MES ou ERP permettent de piloter au plus près chaque étape. Les indicateurs phares (TRS, taux de qualité, gestion des arrêts) s’affichent en temps réel, accessibles à tous. La moindre dérive déclenche une action corrective sans attendre. Et la durabilité environnementale s’impose : baisse des consommations d’énergie, tri des déchets, traçabilité renforcée. La performance industrielle d’aujourd’hui s’ancre dans une nouvelle réalité, attentive à l’environnement de travail comme aux attentes de la société.
La performance industrielle ne s’arrête jamais vraiment : chaque progrès en appelle un autre, chaque innovation rebat les cartes, chaque acteur de l’usine peut devenir le déclencheur du prochain saut de compétitivité. Qui relèvera le défi demain ?
-
Actuil y a 6 mois
Les alternatives légales à French Stream : ce que vous devez savoir
-
Actuil y a 6 mois
Les prénoms les plus rares au monde et leur origine
-
Familleil y a 1 an
Identification des signes révélateurs chez l’enfant haut potentiel
-
Modeil y a 8 mois
Talons confortables : choix et conseils pour un bien-être optimal